How to choose the plastic manufacturing process correctly?
Before ordering the production of plastic parts, you should know well how to choose the relevant process and what factors to consider in this regard. Therefore, in the following, we will describe some of the most important parameters that you should pay attention to while choosing the production process.
Budget and cost: First of all, you should measure the amount of budget you have available to produce the relevant parts and set up your production line accordingly. Normally, with the increase or decrease of production volume, the production cost of each piece does not change much.
The shape of parts: Another point that plastic parts manufacturers should keep in mind is the model of the production part. That is, they should clearly determine the complexity of the production of this piece. The more open the designer's hand is in optimizing the production of the part, the lower the final costs will be.
Quality: The resistance and strength of the product you produce must be suitable for its application. It means that it can be well resistant to the stresses that are applied to it in various industries during the production of devices and tools.
Duration: Finally, you should keep in mind the approximate duration of your orders and know well how much time it will take to produce a specific piece in a certain volume.
All kinds of plastics
Knowledge of various types of plastic materials led to the creation of the idea of producing plastic parts in the modern industry, and today, many manufacturers of parts for various devices use this material, which is cost-effective and more durable. Therefore, as a producer or orderer of plastic parts, you must get to know the types of plastic used in this industry and obtain sufficient information about the advantages and disadvantages of each of them. So stay with us to learn about thermoplastic and thermoset (the main plastics used in the plastic parts manufacturing industry). Thermoplastic: This material is produced in the form of sheets or small pellets in the heating process and it is possible to recycle it. Some of the most common items used in the production of thermoplastics are: polyvinyl chloride, polyethylene, polypropylene, acrylonitrile butadiene styrene, polyamide, acrylic, polycarbonate. Thermoset: Compared to thermoplastics, thermoset plastic remains in a solid state after production and is not reversible. Because when heated, instead of melting, they decompose and do not change state after cooling. Some of the most common materials used in the manufacture of thermostatic plastic are: phenol formaldehyde, urea formaldehyde, cyanate ester, epoxy, polyester, polyurethane, silicone.

The stages of making and producing plastic parts
To make and produce plastic parts, first thermoplastic is melted in the injection section of the machine. Then, the materials are poured into the device in specific proportions through the funnel and are melted by heating. After that, it should be injected into the cylinder funnel, and from there, it will be gradually directed towards the outer and inner mold and injected between these two molds, so to speak. Finally, after the material has cooled, the moving part of the mold is separated and the plastic piece is removed from it.
Types of plastic production processes
The types of production process of plastic parts are divided into several categories: Vacuum forming: In this method, plastic is poured into the mold and heated. During this process, a variety of vacuum forming devices are also used to shape the materials. Plastic injection: It is the most common method of producing plastic parts. In this method, the melted raw material is poured into the mold and after cooling, it will be separated from the mold. 3D printing: The 3D printing method or attention to the type of material used will be different. For example, if plastic filament is used, the printing method will be FDM. For liquid resin and plastic powder materials, SLA and SLS printing methods will be used, respectively. CNC machining: In the machine cutting method, we will not have the plastic melting process, but solid plastics are cut and shaped using CNC machines. Polymer casting: This process is done using chemical reactions, and the basis of its work is the use of rubber material or reactive liquid resin. Rotational molding: If you want to produce large hollow plastic parts, the rotational molding process will be efficient. In this method, the use of thermoplastic material is more common than thermostat. Extrusion: In this method, molten plastic is directed towards the mold and after passing through the mold with pressure, it takes the final shape of the corresponding part. Air molding: This method is also used to make hollow plastic parts, which is based on blowing compressed air into the mold through a plastic tube.
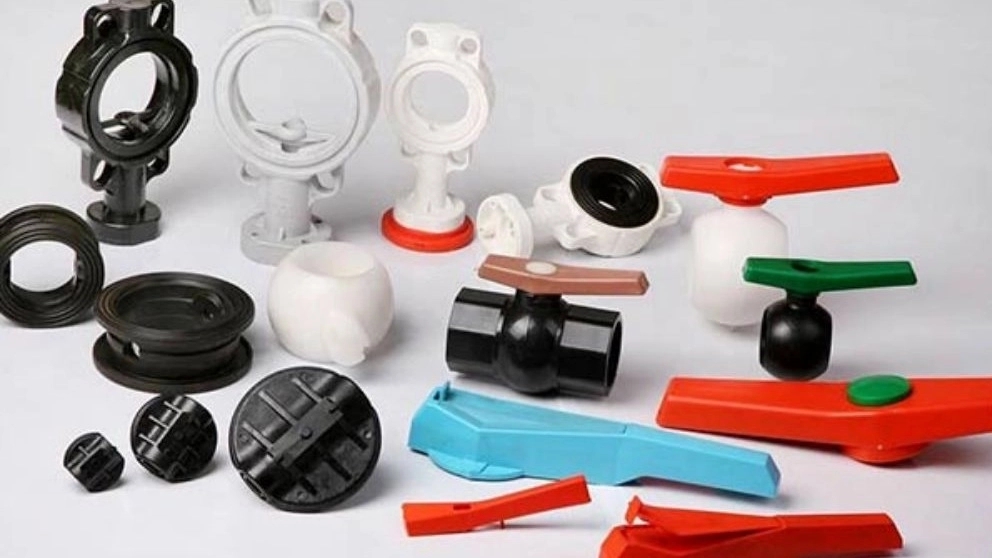
Fast manufacturing of plastic parts using 3D printing technology
As we mentioned a while ago, 3D printing is a method of making plastic parts that is used in many types of plastic parts production workshops today. In this way, printing software plays an effective role. In fact, with the help of this tool, the shape and mode of cut is determined and the necessary support structures are added. Besides, according to the type of material, the printing style is divided into FDM, SLA, SLS category. Finally, after the completion of the operation, the prepared parts are separated from the printer and the final baking is done if necessary, and the support structures are removed.
Groups of plastic parts that can be produced with a small injection machine
So far, you have learned about the types of plastic parts production machines, now it's time to know what types of parts can be produced using a small injection machine?! Join us to find the answer to this question. Among the plastic parts that can be produced with an injection machine are:
Paint industry buckets and cans
Military industry connectors
Parts of the cockpit and food storage compartment in the plane
Plastic parts in communication industries such as mobile phones, computers, etc.
Industrial machinery parts
Plastic speed limiter and traffic lights
Home appliances such as seeds, pots, door and window parts, etc.
All kinds of water and sewage rubber washers
Plastic toys

What are the most important reasons for producing plastic parts?
So far, we have noticed that in the main part of the production of various parts, plastic material is being used. That's why you may have this question, what is the main reason for the popularity of plastic material in the parts manufacturing industry?! In response to this question, the following points can be mentioned:
The durability of plastic is higher than some other materials.
The speed of production of parts increases with the use of plastic material.
The total cost of the production process using plastic materials is lower.
The amount of waste and waste in this industry is less than the production of parts using metal materials, etc.
It is possible to recycle many plastic parts and it can be turned into another product.
The importance of making plastic parts
Using plastic material in manufacturing parts increases work efficiency and saves time. Also, final costs and post-production waste are reduced and raw material consumption is optimized. The possibility of recycling these parts has made it possible to use the same material in different forms several times. The price of plastic is more affordable than other consumables in the industry. Plastic has high durability and longevity, which is also a positive point for the parts that are produced with this material.
Production steps of plastic parts using injection molds and air molds
In the process of producing plastic parts using the method of injection molds, the mold must be prepared first, which is done manually or robotically. In the next step, you should pour the melting material into the mold and so-called injection. After the piece has cooled enough, take it out of the mold and separate the pleats and channels from it.
In the method of air molds, molten material is made into plastic tubes. Then the pipe is placed inside the mold and by blowing with it, the plastic pipe takes the shape of the mold. When the piece is well cooled and formed, it is removed from the mold.